An essential goal in the commercial production of fuel cells is to establish manufacturing processes that are as cost-efficient as possible – starting with testing facilities for in-house research and product development.
At the heart of every polymer electrolyte membrane fuel cell (PEMFC) is the membrane electrode assembly (MEA). Roll-to-roll processing techniques promise the highest savings potential for MEA production, inspection, and quality control. In addition, rising demand for PEM fuel cells and an ever-increasing degree of automation are bringing prices down further.
These also play a crucial role in extending the lifetime of fuel cells. Thus, inline quality control in the production of fuel cell components is as important as it is for companies to carry out a wide variety of trials and tests. Researchers and manufacturers can evaluate results on so-called self-sufficient test facilities.
With a testing facility for membrane electrode assemblies to inspect and test membrane coatings, in particular, Printum Technology GmbH bridges the gap between research and industrial production. Read more below.
Testing Membranes and Coating Materials for Fuel Cell Production
The MEA testing facility was developed in Ravensburg, Germany, to provide an offline test environment for catalyst-coated membranes. It allows fuel cell manufacturers to test new materials in a roll-to-roll process, optimize manufacturing processes and develop innovative products to keep up with a relatively new but highly competitive market that offers vast growth potential.
Our new testing equipment examines, for example, the quality of catalyst-coated membranes and detects damage, such as cracks and pinholes. In addition, a high-precision rewinder enables the integration of different testing methods such as AOI, X-ray or layer thickness measurements, etc.
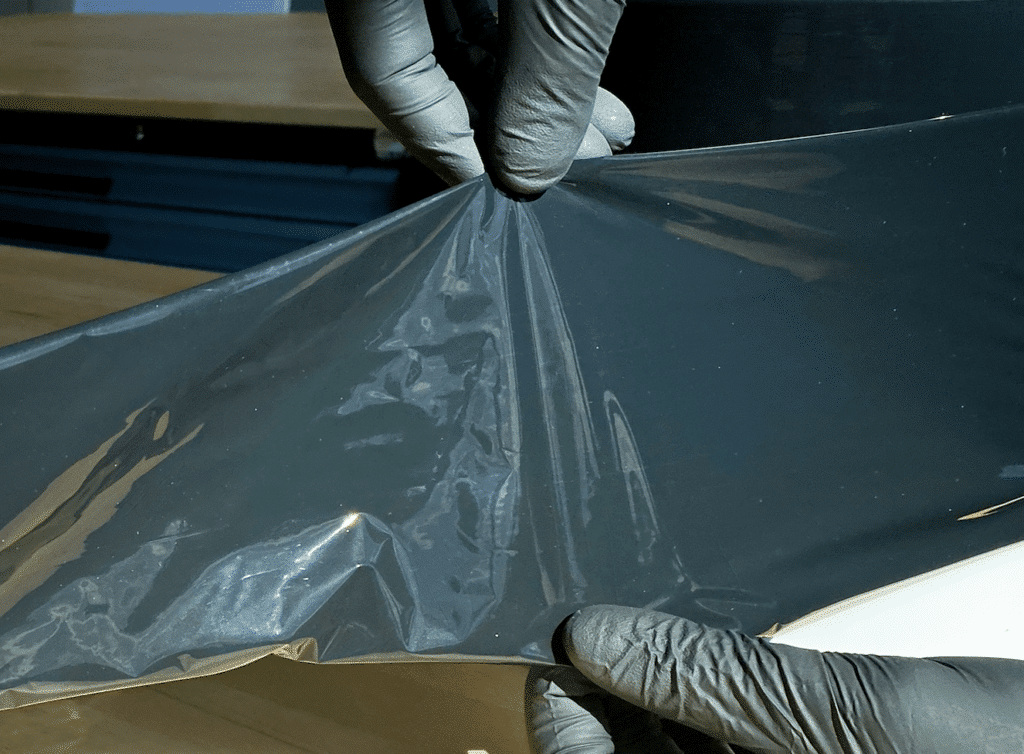
A picture of our test membrane with artificially induced damage in the catalyst coating, such as holes in the micrometer range that are not visible to the naked eye. A unique camera system can scan and code these.
This benefits fuel cell manufacturers, reacting quickly to dynamic market changes. For example, customized testing facilities tailored to different producers’ needs can be used for membrane manufacturing in the medical sector or lithium-ion battery manufacturing for electric cars.
As a system integrator and web handling specialist, Printum thus contributes to the industrialization of fuel cell manufacturing. Read more about the technical details below.
Challenges in Fuel Cell Manufacturing
Hydrogen is a carbon-free fuel source; water is the only by-product of power generation inside a hydrogen fuel cell. This clean way of generating electricity makes polymer electrolyte membrane fuel cells or proton exchange membrane fuel cells (PEMFC) worthwhile for many industries.
In some areas, fuel cells are already being used – for example, in aerospace, transportation, and shipping – to power remote homes in many rural areas of Japan. In the future, fuel cells will eventually become the primary choice for powering vehicles. However, until then, fuel cell manufacturers still have to go over a few things…
1. Extend fuel cell lifetime
Until then, fuel cell manufacturers still have to evaluate how to extend fuel cell lifetime. Fuel cells are often described as a more sustainable alternative for power generation. But, regardless of the application, fuel cells must deliver energy reliably over a long time to meet this expectation.
2. Improve fuel cell manufacturing processes
The performance and service life of a fuel cell depend on the quality of the components used in their production: Thus, for future commercialization, manufacturing processes of fuel cell components need to be improved – especially in terms of their sustainability and cost efficiency.
3. Increase performance
For example, PEMFC technology requires susceptible ion exchange membranes to convert chemical energy into electrical energy. Mechanical properties of the ion exchange membranes, such as robustness and stability, thickness, and uniform coating with a reactive catalyst material, directly impact the efficiency and lifespan of a fuel cell.
4. Improve membrane technologies
Keyword MEA. One way to progress in this promising market segment is to develop high-performance testing procedures for fuel cell components such as the membrane electrode assembly (MEA). Even tiny, superficial cracks and holes in the sensitive catalyst-coated membrane can significantly impact a fuel cell’s service life and efficiency.
Test facility for MEA: Producing high-quality membranes
The MEA is the heart of a PEMFC fuel cell. Most commercially available proton exchange membranes are made of polymers. An ultra-thin catalyst layer is applied to both the anode and cathode sides of the polymer membrane, where oxidation and reduction occur, respectively.
How a catalyst-coated membrane works
The multilayer catalyst-coated membrane (CCM) is a central component of the PEMFC and is produced by manufacturers such as Nafion.
Hydrogen ions are transported through the CCM, which is not only the central enabler of the direct conversion of chemical energy into electrical energy; it also spatially separates the two gases (hydrogen and oxygen) from each other, so it doesn’t produce oxyhydrogen gas.
The central property of the CCM, which allows PEM fuel cells to generate electricity, is its semi-permeability: Only ions of a specific size can pass the membrane, in this case, hydrolyzed protons. Larger gas molecules, on the other hand, cannot get through.
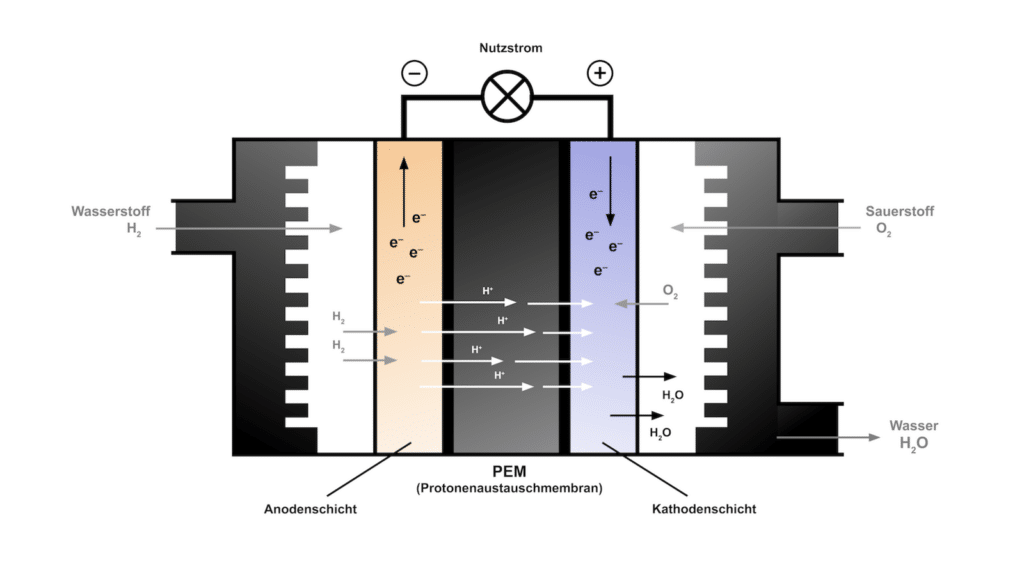
Schematic representation of the structure and function of the catalyst-coated polymer membrane in the PEMFC: Our MEA testing facility ensures that the membrane and its coating is intact and that there is no damage such as holes or cracks that could disturb the chemical equilibrium and, in the worst case, lead to an oxyhydrogen reaction in the fuel cell.
So, as long as a fuel source is available and the individual components of the fuel cell are intact, it can reliably generate electricity. However, small holes, superficial cracks, or comparable irregularities in the delicate membrane can significantly impair the chemical reaction inside a fuel cell.
Moreover, it can impact the performance and lifetime of an entire fuel cell stack. Major damage could also have an impact on the safety of a fuel cell.
The aging process: What happens when a membrane is damaged?
Thanks to studies of the aging processes in fuel cells, however, we know that even the most minor irregularities in the catalyst-coated membrane can have fatal consequences: They set a vicious circle in motion, at the end of which is the death of the fuel cell.
Studies of the aging processes in fuel cells show that water – the by-product of the chemical reaction – is responsible for the cell’s aging. However, it is not always present in the same quantity, as fuel cell cars, for example, produce different amounts of electricity when driving through the city.
The polymer membrane is also exposed to fluctuations of water and humidity: The constant shrinking and swelling of the membrane gradually lead to deformation. As a result, wave-like irregularities and weak spots in the coating are slowly developing. Over time, they turn into tiny holes and mark the beginning and end of a fuel cell.
If the process continues, the holes become more extensive until hydrogen molecules eventually migrate through the membrane (originally impermeable to gas molecules) and react with the oxygen at the cathode. In the process, they form highly reactive radicals that can react with the carbon chains in the polymer membrane and promote inevitable corrosion.

A platinum-coated polymer membrane produced by Nafion – with artificially induced scratches and pinholes in the micrometer range, which can significantly impair a fuel cell’s efficiency and service life.
Holes in the membrane grow more expansive; more gas molecules wander through the perforated membrane. More and more aggressive reactions produce more radicals, and so on. Finally, at the end of the degradation process is the well-known combustion reaction of the oxyhydrogen mixture, which releases so much heat that the membrane melts.
Under normal conditions, these holes develop very slowly. Therefore, detecting mechanical damage that can accelerate the aging process even before the MEA is installed in a fuel cell can prevent premature oxyhydrogen death and helps ensure the performance of the entire PEMFC stack in the long term.
X-Ray images of degradation tests on membranes from the Paul Scherer Institute prove that the aging process is taking place as described in this German article: Vom Nadelloch zum plötzlichen Tod: Wie Brennstoffzellen altern
Testing catalyst-coated membranes and coating materials
This is precisely why self-sufficient testing facilities for membranes and other carrier films will play a crucial role in the future of commercially available fuel cells. In addition, roll-to-roll processes for inline and offline quality testing will play a key role in fuel cell manufacturing. Material testing of the membrane electrode assembly can help save resources and significantly reduce production costs. At the same time, the efficiency and durability of the end product will increase.
Our MEA testing facility allows for the inspection of different coating materials. It recognizes irregularities and mechanical damage that can reduce the service life and efficiency of the cell.
Our top engineers’ most significant challenge was ensuring the particularly gentle and exact web handling of the fragile membrane with sensitive coating.
The current version of the test facility is a customized design for MEA material testing that offers placeholders for further test procedures; among other things, an extension for measuring the coating thickness of a membrane could be easily integrated.
The testing facility has a much more comprehensive range of applications, though. For example, it can also be used for product development in membrane manufacturing for pharmaceutical technologies in the medical sector. In addition, it can be used in lithium-ion battery production for electric vehicles. Read more below.
“The rotary processing of a system of this kind must be seamless and frictionless to prevent damage to the sensitive coating due to friction in the installation itself. To master this challenge and develop a suitable technology, I had to do a lot of research to use all the magic tricks of material science. I bet no one will copy this shortly.” |
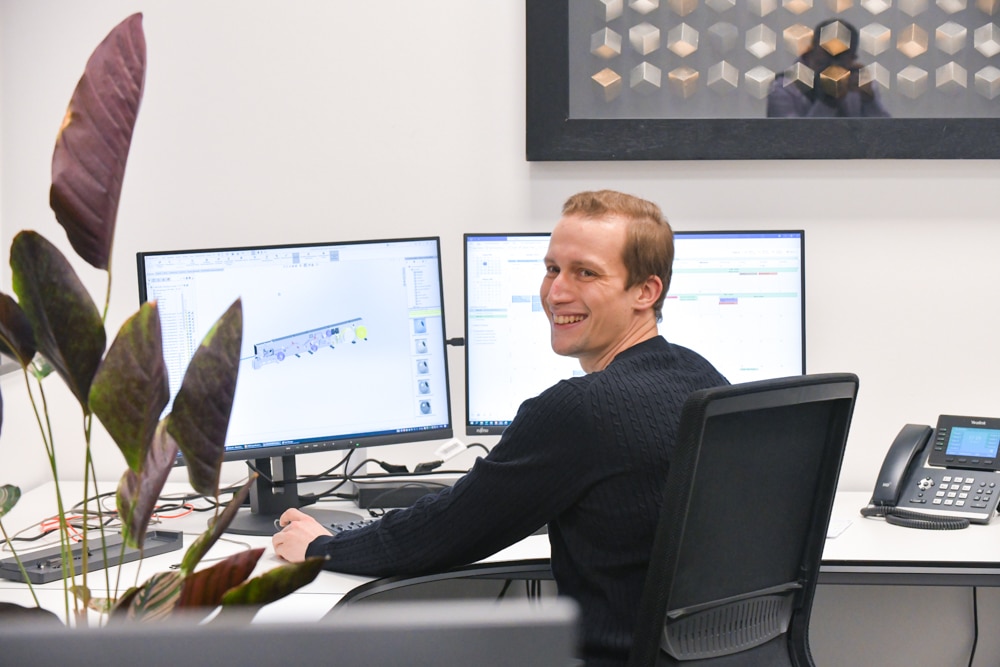
Christopher Bétrémieux, Construction Engineer at Printum Technology GmBH in Ravensburg, Germany
Other areas of application: Lithium-ion battery production
Energy storage is another critical future technology for the automotive industry and the expansion of renewable energies. Lithium-ion batteries are a key to storing electricity from sustainable sources such as PEMFC or other fuel cells that can generate electricity but not store it.
Similar to the MEA, the central unit of a lithium-ion battery consists of an anode and cathode and a microporous separator that separates the two electrodes. Between them is the electrolyte. During electrode production, the top and bottom of the carrier film are coated with an electrode slurry. Even when mixing the electrode slurry for coating, it is essential to avoid contamination of the material by penetrating foreign particles.
Other essential parameters and quality characteristics in battery production:
- the cleanness of the substrate,
- the precisely defined porosity of the separator,
- the layer thickness accuracy,
- the surface quality, and
- the surface structure.
Printum special machinery for battery production
Evaluating production processes and their results, as well as developing new materials for lithium-ion batteries, require cost-effective production tests. This usually involves adjusting equipment to different electrode slurries to obtain the best possible coating result.
In addition to continuous inline quality monitoring during production, our stand-alone test system can also be used in battery production to check the result after adjusting the system parameters and to make production tests more efficient in the offline roll-to-roll process.
The test results are available immediately and enable rapid evaluation: quality data for different material variants and individual production steps and the adjustments made increase the efficiency of product development, production, and subsequent commercialization. The agility gained also makes it possible to respond quickly to dynamic effects on the market and fluctuations in demand.
Summary
With our test facility, we bridge the gap between research and industrial automation – a decisive contribution to fuel cell manufacturing and product development. The MEA testing system detects and marks superficial damage on the catalyst-coated membrane, enabling efficient material testing of the membrane-electrode assembly before further processing.
Thus, thanks to intelligent processes, fuel cell, and membrane manufacturers benefit from an efficiency gain. Finally, they make their end customer happy by providing them with a high-quality fuel cell with a long lifetime – thanks to the roll-to-roll testing facility of Printum Technology GmbH.
Lastly, customized solutions for material testing also get battery production rolling, as developing new materials for lithium-ion batteries requires similar testing procedures.
Coming to an end, there’s only one thing left to say, and that is: Long live the fuel cell (and the battery).